Automotive, heavy-duty transportation, and stationary energy storage industries are trying to identify the best technology lithium-ion battery solution to meet their goals and market share targets. There are many factors to be considered, such as raw material selection, cell format and configuration, module architecture, and battery pack design.
When analyzing the basic and first technical aspect, the raw materials, the industry continues to spend several billions of dollars yearly in R&D trying to identify the best, more abundant, and safer materials for lithium-ion cells for the long term. However it is still necessary to take actions today to address current market demands.
Meanwhile, for the short term, major OEMs and companies in this industry must pick between solutions available today and adapt them to fulfill end-user application needs. It leads to a non-standardized market, high variances and discrepancies between technologies, and higher cost.
The most common lithium ion battery technologies today uses Carbon (graphite) in the anode. Analyzing cathode raw materials, the most commercially used are: LFP (lithium-iron-phosphate), NMC (nickel-manganese-cobalt), and NCA (nickel-cobalt-aluminum). They have different properties, energy density, charge/discharge rates, life cycle, safety, temperature tolerances, and, consequently, are best suited to different markets.
There is no ‘one fits all’ option, there is no “preferred’ li-ion battery cell chemistry technology yet. Different applications have different requirements, and new advancements and improvements are still under development.
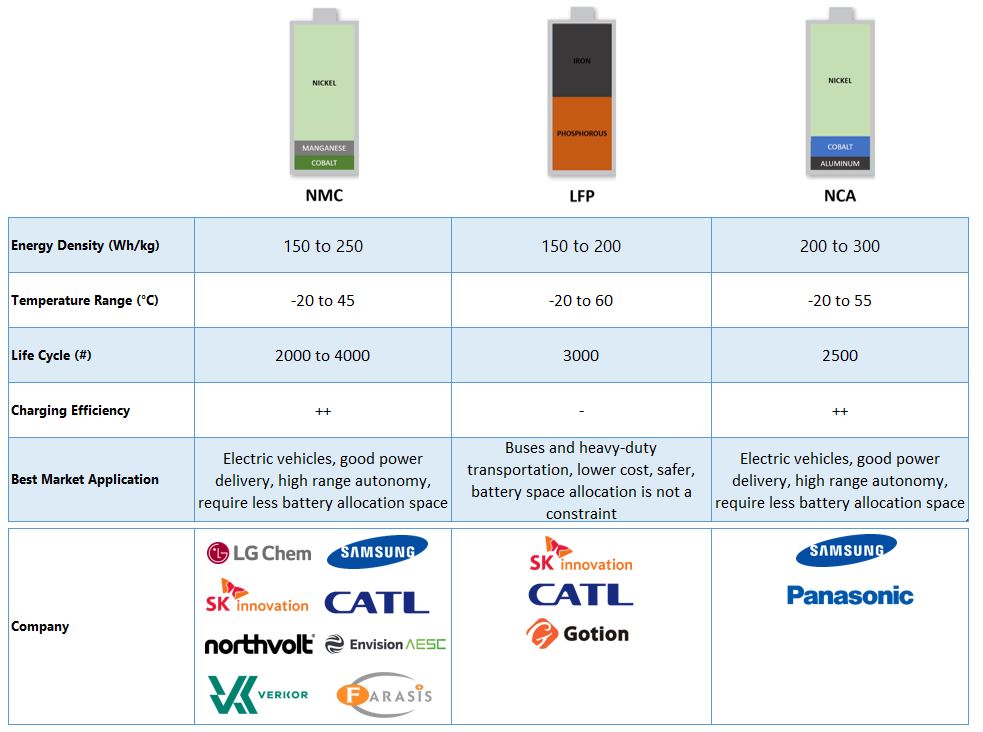
LFP batteries are the most used in the Chinese market, and most Chinese companies manufacture this type of lithium-ion cell. This is due to the large supply of raw materials on Chinese land, a factor that may limit the adoption of this technology in other countries. Its energy density (capacity to store energy per kilogram of lithium cell) is relatively low, between 150Wh/kg and 200Wh/kg. This directly impacts batteries weight. However, its chemical stability is an excellent property, being able to operate safely between -20°C and 60°C with minimal risk of exothermic events (also known as ‘thermal run-away’). The life expectancy reaches 3000 life cycles, a factor that directly depends on the operating conditions throughout the battery life. On the other hand, charging efficiency is lower than its competitors, implying a slightly higher cost to charge batteries, and more time required for recharging events. Regarding market applications, LFP is a good option for large vehicles and cargo transport, such as buses, trucks, rail, stationary applications, and other applications that require low price, and where the dimension is not a restrictive factor.
On the other hand, NMC batteries have a higher energy density, between 150Wh/kg and 260Wh/kg, and a lifespan between 2000 and 4000 life cycles. Note that expected life can be multiplied by more than 3 times, reaching over 12000 cycles, depending on the depth of discharge (DoD) and operating temperature, maximum cell charge voltage, among other factors. A limiting factor is a higher instability of operation for temperatures above 45°C, which increases the risk of fire if an effective thermal management of the battery does not act. They have greater charging efficiency, minimizing losses during each charge, and less time required for 100% battery charge. Due to their high energy density, NMC battery is a good solution for small vehicles and passenger cars which have limited space for batteries, offer a long autonomy between charges, good power delivery (torque), and can also be good solutions for stationary systems. However, they face prices fluctuation for cobalt and manganese materials in the global commodity market in recent years, in addition to humanitarian factors and poor working conditions which can affect countries and populations, especially in Africa.
Lastly, NCA batteries have similar performance to NMC batteries. This technology is widely used by Tesla, and has an energy density that can reach up to 300Wh/kg. They also have good thermal stability up to 55°C, and a service life of around 2500 charge and discharge cycles. It is worth mentioning that due to the configuration of Tesla’s battery management software (BMS – Battery Management System), this lifespan can also be increased by more than 3 times. Vehicle software “limits” the maximum depth of discharge (DoD), and the maximum charging voltage, factors that maximize the life of the battery cells. They feature high charging efficiency, excellent power (torque) delivery, and enable long journeys and high vehicle autonomy. They are good options for the stationary energy sector, but they may present little availability for this sector due to their large-scale use in the automotive sector. Analyzing materials prices in the global commodity market, aluminum and cobalt have shown high fluctuations in the market, a factor that directly impacts the final price of battery cells. NCA batteries also share restrictions on humanitarian aspects and poor working conditions in cobalt extraction countries in Africa.
Facing these challenges, cell manufactures are developing two technologies in parallel trying to position themselves in the market today and increase their market share. Weaknesses of one technology can be the strength of the other.
Therefore, cell manufacturers and companies in this industry are closely watching raw material scarcity and their impact on the battery price, material recyclability, and geo-political and humanitarian constraints to extract and buy raw materials for lithium-ion batteries. These critical factors will define which battery cell technology will be better adopted by users in a medium- and long-term perspectives. And to the battery market even more competitive, solid-state lithium cells are under development, and will soon be available in large scale volume to compete in various markets.